В промышленных масштабах в основном производят две группы термоэластопластов: смесевые и динамически вулканизированные. Да, есть ещё блок-сополимеры, но в интересующей нас сфере они почти не применяются, да и глобально их доля относительно мала.
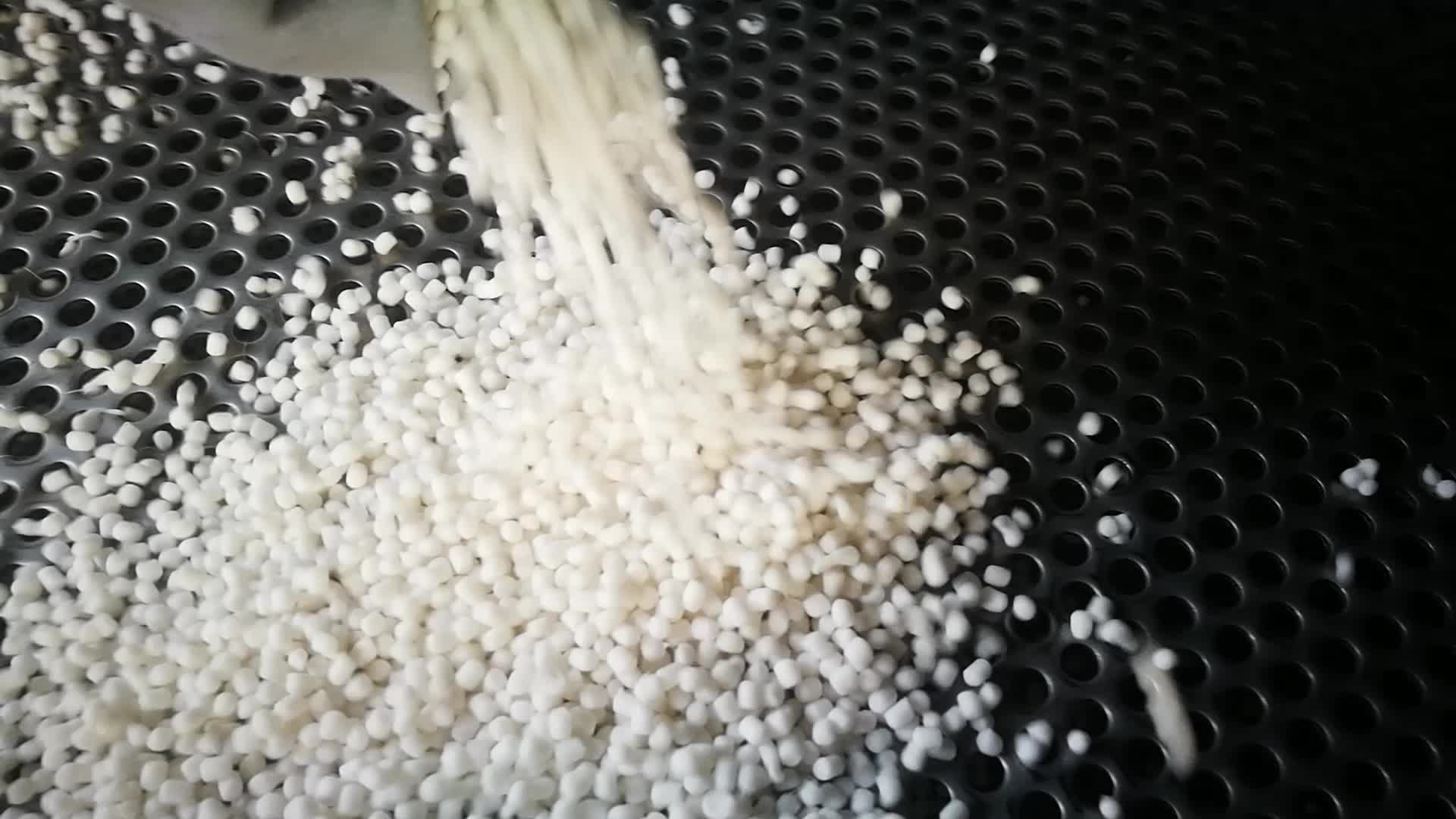
Смесевые термоэластопласты
Смесевые термоэластопласты получают высокоскоростным смешиванием термопластов с эластомерами при высокой температуре. Тонкая настройка условий, при которых происходит смешение, и соотношения компонентов, которые смешиваются, можно варьировать свойства получаемого материала, добиваясь подходящих результатов для конкретных задач. В этом методе наибольшую популярность в качестве основного компонента термопластичной фазы обрели поливинилхлорид, полипропилен и полиэтилен. Смесевые ТЭП имеют свои преимущества, но у них низкая устойчивость к воздействию агрессивных сред, высокая ползучесть при нагрузках и проблемы с высокоэластическими свойствами. Поэтому главный героем этой статьи стал термопластичный вулканизат.
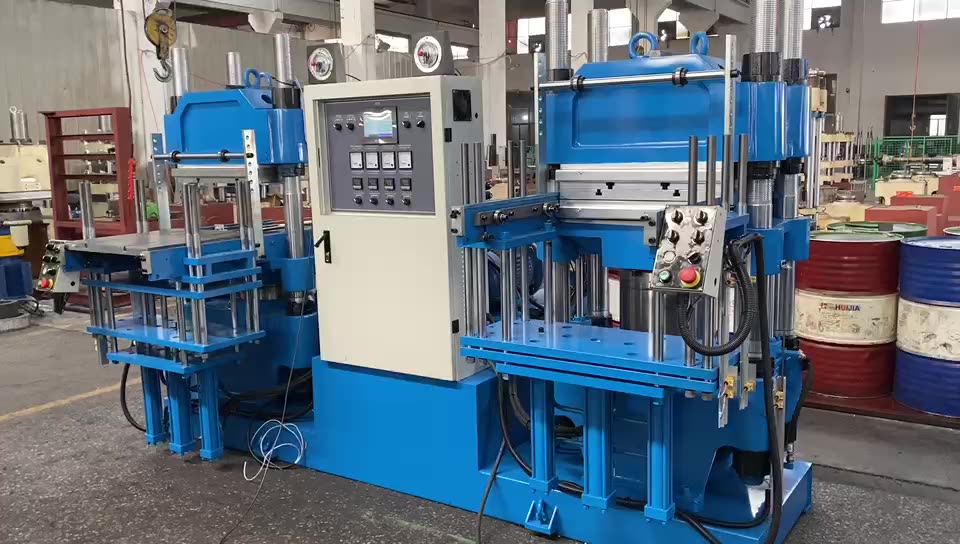
Динамическое вулканизирование
Главная особенность TPV — при тех же высоких скоростях и температурах с процессом смешивания совмещают и процесс вулканизации, вводя в состав специальные компоненты. Это могут быть диметилолфенолы, пероксиды, фенолформальдегидные смолы и другие разнообразные вещества — каждый агент вулканизации имеет свои особенности и влияет на свойства получаемого в итоге ТПВ.
Но самое важное — вулканизация определяет саму структуру вещества. Смесевые термоэластопласты представляют собой матрицу с диспергированным эластомером, а в TPV в фазе термопласта равномерно распределены сшитые частицы эластомера. И если в первом случае со временем может происходить так называемое «слипание» частиц дисперсной фазы, то вулканизация позволяет создать стабильную структуру, при которой материал будет сохранять все свои качества и свойства. Более того, даже низкая степень сшивания, по сравнению со смесевыми композициями, значительно повышает сопротивление агрессивным средам, усталостную прочность, предел прочности при разрыве и снижает остаточную деформацию.
Производство ТПВ также можно разделить на два основных типа: с периодической схемой и непрерывной.
При непрерывной схеме производства всё происходит в однонаправленном двухшнековом экструдере, имеющем сложную форму червяка, высокое соотношение длины к диаметру (L/D не менее 40:1) и большое количество рабочих зон. Температура процесса такого производства обычно находится в промежутке от 170 до 220°C. Без дегазации в таком производстве обойтись невозможно.
Другой вариант — периодическая схема производства. В этом случае используется резиносмеситель, в котором готовят маточную смесь из каучуков с различными технологическими и защитными добавками, а также вулканизирующих агентов. Потом к этой смеси в экструдере добавляются компоненты фазы термопласта, это происходит при температурах, позволяющих расплавить термопласт — так происходит вулканизация, гомогенизация и, наконец, грануляция материала.
Как вы могли понять из этой статьи, создание TPV-крошки может происходить различными способами и с использованием различных материалов, таким образом появляется множество модификаций этого продукта, среди которых обязательно найдётся тот, что идеально подойдёт для ваших задач.