Если говорить простым языком, то старый стирол-бутадиеновый каучук измельчают до маленьких кусочков, а потом из этих кусочков делают такие уже привычные для нас резиновые покрытия. Но если углубиться в детали этого процесса, то окажется что всё гораздо сложнее и интереснее.
Дробление
Действительно, основным процессом для получения крошки является дробление, но происходить это может самыми разными способами, используя режущее, сдвиговое деформационное, электромагнитное, ударно-волновое, ультразвуковое, взрывоциркуляционное или даже лазерное воздействие.
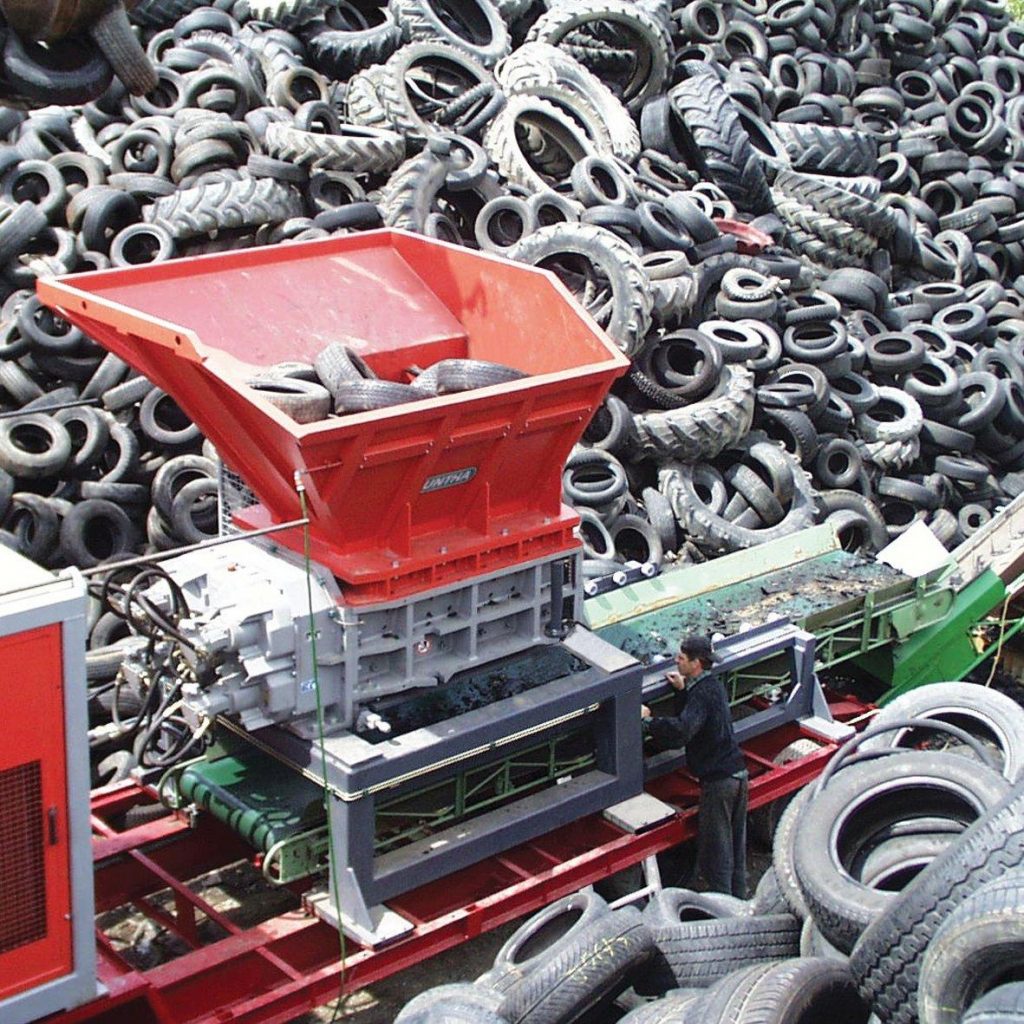
Самым популярным и эффективным считается старый добрый метод механического измельчения, в этом случае каучук сохраняет свои молекулярные свойства и на выходе получается резиновая крошка высокого качества. Сначала из покрышек на вырубном станке вырезают бортовые кольца. Потом покрышки режут на ленты, для этого используют гильотины, гидравлические ножницы или механические резаки. После этого начинается получение полезных материалов.
На первом этапе дробления образуются так называемые чипсы фракцией от 10 до 50 мм с максимальной насыпной плотностью (около 500 кг на м³). Такой материал можно использовать для создания нижнего слоя покрытий или как наполнитель для дорожных ограждений.
Потом идёт доработка сырья до нужной фракции, если нужно получить именно гранулят. Это делают при помощи роторных мельниц с четырёхгранными ножами. Так получается SBR-крошка фракцией от 3 до 10 мм. Но в ней остаётся мусор от покрышек: металлический корд, текстильные волокна и другие посторонние включения. Для того, чтобы избавить от них нашу крошку, используются магнитные и воздушные сепараторы. В конце, при помощи вибросита, полученный материал сортируют по фракциям.
В этом методе стоит отметить один неочевидный момент: фракция крошки зависит от режущих элементов станка, на котором её производят.
Шредерные машины выпускают кубическую крошку от 3 до 5 мм, а дисковые ножи подходят для создания фракции от 1 до 3 мм.
Заморозка
Но и на этом тонкости не заканчиваются. Дробление можно осуществлять при низких температурах, в диапазоне от -60℃ до -90℃, в таком случае в производстве используется жидкий азот или турбохолодильные машины. Это позволяет сделать резину более хрупкой, что позволяет легче отделять металл и текстиль, а также снижает энергозатраты на производство.
Давление
Другой вариант — использование высокого давления, в этом случае псевдосжиженная резина стекает через отверстия специальной камеры.
Озоновый нож
Ещё одно интересное решение, будто пришедшее из фантастического фильма, это «озоновый нож». Автомобильные покрышки теряют углерод-углеродные связи в озоносодержащей газовой среде, а выглядит и работает это, как если бы мы ускорили время в одном конкретном помещении — по сути резина очень быстро стареет и саморазрушается в крошку.
В общем, когда вы в следующий раз увидите пособие по производству резиновой крошки в домашних условиях своими руками, крепко задумайтесь, что именно может получиться и какого оно будет качества.